Welding an O2 bung...
#1
Launching!
Thread Starter

Not knowing much about welding, yall think it's OK to braze weld an O2 sensor before the cat just after the manifold? My buddy has a wire feed machine with flux core but he thinks brazing will do a better job. Trying to do this myself instead of going to an exhaust shop, and I need my truck back on the road for monday.
Those damn manifold bolts are a PITA
Those damn manifold bolts are a PITA
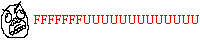
#3
TECH Senior Member
iTrader: (45)
Join Date: Jun 2005
Location: Hennessey, Oklahoma
Posts: 9,439
Likes: 0
Received 11 Likes
on
5 Posts

If you know how to actually use a flux core welder it will be to tell between a flux core and gas mig welder. If its a cheap little Lincoln set it on "B" heat range and "3" wire feed and go really slow.. People tend to go fast like you can on gas mig and that's when it looks like ****..
#4
Praise The Lowered
iTrader: (17)

Because the bungs are pretty thick/exhaust thin, I would turn it up high and put the wire speed low, start the puddle on the bung and drag it to the pipe (quickly back to bung after penetration),repeat while always keeping a puddle of red hot metal/wire..FyI flux core is what we use at work in structural applictions..If you all want a cleaner better weld try 232 wire as opposed to the 211mp everyone uses....good luck
#5
Launching!
Thread Starter

Well we decided to stick weld it, to protect the threads I threaded a bolt in the fitting...one it was welded up I took the bolt out no problem. Went to screw in the wideband and the threads got trashed 
So one trip to harbor freight and a tap & die set later, I got everything put back together. I'm glad I tried to install the sensor while the Y was still off the truck first.
Shoulda just got me a set of headers to install lol

So one trip to harbor freight and a tap & die set later, I got everything put back together. I'm glad I tried to install the sensor while the Y was still off the truck first.
Shoulda just got me a set of headers to install lol
#7
Launching!
Thread Starter

Yeah, lesson learned the hard way. Purchased this kit Pittsburgh - Item#41452
Been wanting a set, and I had to have it to get the truck back on the road for today.
Been wanting a set, and I had to have it to get the truck back on the road for today.
Thread
Thread Starter
Forum
Replies
Last Post
Mangled03gmc
GM Engine & Exhaust Performance
6
08-11-2008 02:42 PM